How is Structural Drying for Water-Damaged Properties Done?
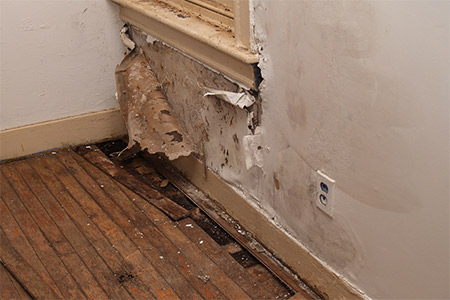
When their house or building has a bad case of water damage, the most common response by the property owner is to demolish the affected area. Yet with today’s technology, demolition is now the last resort. Restoring water-damaged properties is now the first line of action through the method of structural drying.
But how does it work? Here’s a quick overview of the process:
1. Identify and separate the water-damaged area from the dry parts.
On the top of a restorer’s priority is to mitigate the extent of water damage. This is done by identifying the already damaged area using probes and infrared tools. The restorer also looks for the water source to check if other kinds of structural repair—for example, fixing a leaking pipe—are necessary.
2. Evaluate the gravity of water damage.
By assessing, categorizing, and classifying the water damage, restorers will know which cleanup method and equipment to use. This is according to the standards set by the Institute of Inspection Cleaning and Restoration Certification.
For example, there are four classes of water damage, ranging from Class 1 (least amount of water absorbed and evaporated) to Class 4 (specialty drying situations). Meanwhile, there are also three categories of water causing the damage. These are namely Category 1, or a clean water source; Category 2, pertaining to gray water; and Category 3, grossly unsanitary water such as floodwater, sewage, and water contaminated with feces.
3. Clean up and dry the area.
Based on the data accrued during the previous steps, work on the water-damaged area will finally commence. Restorers will use a variety of equipment to clean up and dry the area, such as air movers and dehumidifiers. They will also dry furniture, dispose of unsalvageable items, and deal with other materials damaged inside the structure during this step. This process is called content manipulation.
4. Monitor the area in the succeeding days.
Of course, the drying process won’t be overnight. Equipment installed in
the area will be left to work for a three or four day period, with daily
inspections to determine the status of the area. Workers will check the
place’s temperature, humidity, and moisture content during these
inspections. They will also check if additional measures should be done to
hasten the drying process.
The drying process will only be considered complete when certain criteria
are met.
Due to the special equipment and expertise needed for structural drying, hiring a professional restoration company is a must. For the Little Rock, and Conway areas in Arkansas, Chenal Restoration is the top choice. Call our 24/7 Emergency Response hotline at 501-509-8855 for more information.